Introduction
The purpose of this study was to determine the effects of primer on the strength of solvent welded joints in plastic water distribution and drainage systems.
Solvent welding of plastics is combining two pieces of the same material together into one piece. It is different from an adhesion process in that while the materials never touch in adhesion, and are separated by an adhesive agent ("Adhesive bonding", n.d.), in welding, the two pieces actually fuse together to form a bond as strong as, or stronger, than the original material.
The two types of plastic that will be tested in this investigation are PVC and CPVC. PVC, or polyvinyl chloride, is made up of mostly chlorine and carbon (Johnson, n.d.). CPVC, or chlorinated polyvinyl chloride, is similar to PVC material, but contains a higher amount of chlorine, allowing it to withstand a wider temperature range ("What's the difference between PVC and CPVC pipe", 2012). PVC is used mostly in drain and irrigation systems, and CPVC is used mostly in hot and cold residential water distribution systems.
Both PVC and CPVC plastics are amorphous in composition. This means that they do not have a crystalline structure when they are in a solid state ("PVC's Physical Properties", n.d.). According to "Thermal properties of polymers" (n.d.), "When rapid cooling occurs to a temperature at which the crystalline state is expected to be the more stable, molecular movement is too sluggish or the geometry too awkward to take up a crystalline conformation. Therefore the random arrangement characteristic of the liquid persists down to temperatures at which the viscosity is so high that the material is considered to be solid". These amorphous solids undergo a process known as glass transition at a certain temperature instead of melting ("Glass transition", 2005). The glass transition temperature (Tg) of PVC material is about 84°C, and the Tg of CPVC is about 123°C (Tryon, 1975). At the specified temperature, the substances will become softer and more pliable, eventually becoming a liquid ("Glass transition", 2005).
Solvent welding happens in three steps (Dukane Corporation, 2013). The first step is pressing, and it is required to ensure contact between the two pieces being welded, maintain proper orientation of the pieces and to force intermolecular diffusion between the two pieces. The second step is getting the temperature of the material over its Tg by use of a cement. This is achieved by lowering the Tg of the material until it goes below the temperature of the material. Doing so allows for the polymer chains to diffuse between the two pieces ("What is solvent welding?", 2014). The last step is restoring the temperature of the material back under its Tg. This solidifies the pieces together and ensures that they will not continue to move around, creating a rigid joint between the two pieces (Dukane Corporation, 2013).
The second step of the solvent welding process requires the use of a cement, which is composed partly of PVC (Oatey, 2012). This helps the two pieces of material in that it provides a surface on which the two materials can fuse. It also contains acetone, which softens the materials to ensure maximum joint strength.
In addition to the cement, a primer may also be used during the solvent welding process to presoften the material to fuse and create maximum joint strength (Oatey, 2014). The primer is made of around 20%-40% acetone (Oatey, 2012). According to Hong and Wu (2000), the acetone used in their tests lowered the Tg of epoxy resins during their curing by decreasing the degree of cross-linking. The lowered Tg that the acetone in primer allows for the diffusion of the polymer chains at a lower temperature than would normally be required. Therefore, in solvent welding, the heat normally required by other types of welding is not required ("Thermal properties of polymers", n.d.).
There are two "classes" of cement. According to the manufacturer, one class requires the application of primer, such as All-Purpose cement, Regular Clear PVC cement and Medium Gray PVC cement. The other class does not require the application of primer, such as Hot Medium Blue Lava PVC cement and Rain-R-Shine® Medium Blue PVC cement.
The reason for performing this investigation is that there are disagreements between professional plumbers on the necessity of primers in the process of solvent welding of plastic pipes and fittings. This study will help determine if the application of primer significantly increases the strength of cemented joints.
If primer penetrates and softens the plastic surfaces prior to the application of cement, then the inclusion of primer in the solvent welding process should achieve maximum fusion and strength.
Material List
PVC Compression Test
- 200 38.1 mm 1/2" Sch. 40 PVC pipes (cut and deburred)
- 400 1/2" Sch. 40 PVC tees
- One can (237 ml) of the following cements:
- → Regular Clear
- → Medium Gray
- → Hot Medium Blue Lava
- → Rain-R-Shine Medium Blue
- → All-Purpose
- One can of purple primer
- 3.63 tonne bottle jack
- Adjustable wrench
- 226.8 kg digital scale
- Wooden frame
CPVC Torsion Test
- Vise
- Socket wrench, 22.2 mm hex shaped socket, and size adapters
- Torque measuring adapter
- Forty 1/2" CPVC male adapters
- Forty 38.1 mm 1/2" CPVC pipes (cut and deburred)
- Twenty 1/2" CPVC elbows
- One can of All-Purpose cement
- One can of purple primer
Procedures
How to Solvent Weld
(Refer to this when the below procedures call for solvent welding)
- Identify the two pieces of material to be solvent welded.
- Mark a line on the pipe at 6.35mm (1/4 in) from the end of the pipe to indicate how far the pipe is to be inserted into the fitting.*
- For primed joints only, apply a coat of primer around the outside of the pipe and the inside of the fitting. While the primer is still wet, immediately proceed to step 4.
- Apply a coat of cement around the outside of the pipe and the inside of the fitting.
- Push the two pieces together until the marked line and twist 90°. Hold the joint for 15 seconds to ensure that the pieces do not slide apart.
* The pipe is not fully seated into the fitting socket in order to allow space for it to fail during the
compression test and in order for it to be weak enough to fail for the torsion test.
Compression Test
- Set up the wooden frame and equipment as shown in Figure 1.
- Assemble the wooden pieces together.
- Place the digital scale on top of the base platform, and plug in the digital scale to an electrical outlet.
- Place a wooden plank on top of the scale to distribute the weight of the pressure on the bottle jack evenly.
- Place the bottle jack on top of the wooden plank.
- Place a piece of support wood on top of the bottle jack.
- Take a PVC pipe and solvent weld it to a PVC tee on one end with primer. Then solvent weld it to another tee on the other end of the pipe without primer. This creates a pipe assembly with two solvent welded joints, one with primer application and one without. Refer to Figure 2 for a diagram.
- Wait the designated time before performing tests - either 2, 4, 6, or 24 hours.
- Position the pipe assembly above the wooden block.
- Zero the scale.
- Slowly apply compression against the pipe assembly using the bottle jack until one joint (either primed or unprimed) fails.*
- Record which joint failed and the compression force at which it failed.
- Continue to apply compression until the other joint fails.*
- Record the compression force at which it failed.
- Repeat steps 2 to 9 for all of the PVC pipes, fittings, primer and cements.
- Compile data and results.
- Cut select samples to examine cross sections of joints.
*Joint failure for the Compression Test is when compressed, the pipe and fitting separate at the
joint and the pipe bottoms to the end of the fitting socket.
Torsion Test
- Take a CPVC male adapter and solvent weld it to a CPVC pipe with primer. Take a CPVC elbow and solvent weld it to the other side of the CPVC pipe without primer. Repeat the same process on the other side of the elbow to create a pipe assembly containing one elbow, two short pieces of pipes and two male adapters. This pipe assembly contains a total of four solvent welded joints: two with primer application, two without. Refer to Figure 3 for a diagram.
- Wait the designated time before performing tests - either 2, 4, 6, or 24 hours.
- Set up the equipment as shown in Figure 4.
- Attach the vise to a stable surface.
- Tightly clamp one side of the pipe assembly in the vise while exposing the male adapter end.
- Insert the hex shape CPVC male adapter into the matching size hex shaped socket.
- Attach the torque measuring device to the socket.
- Attach the socket wrench to the torque measuring device.
- Reset the torque measuring device.
- Slowly turn the socket wrench to apply torque until one joint (either primed or unprimed) fails.*
- Record which joint failed and the torque at which it failed.
- Repeat steps 1 to 6 for all of the PVC pipes, fittings, primer and cements.
- Compile data and results.
- Cut select samples to examine cross sections of joints.
*Joint failure for the Torsion Test is when torqued, the pipe and fitting separate/twist off at the
joint.
Results
Compression Test Results
Table 1.1 - Compression Test
Cement |
Primed |
Unprimed |
Primed |
Unprimed |
Primed |
Unprimed |
Primed |
Unprimed |
Primed |
Unprimed |
Average Force |
Compression Force (in Newtons) at Failure After 2 Hours |
Medium Gray |
1664.6 |
2389.6 |
2137.4 |
2077.8 |
1527.1 |
2173.4 |
2178.3 |
2359.8 |
1531.1 |
1756.6 |
1979.6 |
1709.9 |
2162.8 |
1905.7 |
2140.1 |
1661.4 |
2249.1 |
1761.1 |
2155.2 |
2000.8 |
2051.1 |
Blue Lava |
2055.1 |
2302.9 |
1647.7 |
1887.0 |
1659.7 |
1904.8 |
2019.5 |
1091.2 |
1256.7 |
1575.6 |
1740.0 |
1684.6 |
1851.4 |
1741.5 |
1745.5 |
1698.4 |
1719.3 |
1689.5 |
1770.0 |
1824.7 |
1674.8 |
Regular Clear |
1799.3 |
1944.4 |
1576.9 |
2370.9 |
1334.1 |
1579.2 |
1170.4 |
1071.6 |
1522.7 |
971.5 |
1534.2 |
1452.8 |
1640.5 |
1387.9 |
1670.8 |
1678.3 |
1639.2 |
1506.6 |
1490.6 |
1378.5 |
1496.9 |
Rain-R-Shine |
1636.1 |
1873.6 |
1895.0 |
1963.0 |
1169.5 |
1666.8 |
996.9 |
2075.1 |
1635.2 |
1707.3 |
1634.8 |
1286.5 |
1845.6 |
1411.9 |
1797.6 |
1338.1 |
1839.8 |
1540.9 |
1812.7 |
1484.4 |
1990.2 |
All Purpose |
2196.6 |
2373.6 |
2194.8 |
1922.1 |
1329.2 |
1201.1 |
1193.5 |
929.3 |
1532.4 |
2389.6 |
1726.3 |
1719.7 |
1795.3 |
1510.2 |
2144.5 |
1638.8 |
1515.5 |
1770.0 |
1833.1 |
1808.7 |
1528.0 |
Compression Force (in Newtons) at Failure After 4 Hours |
Medium Gray |
2345.6 |
1588.5 |
2350.0 |
2378.9 |
1851.4 |
1632.1 |
2067.1 |
2173.4 |
2269.1 |
2394.1 |
2105.0 |
2105.8 |
1843.8 |
2080.0 |
1925.2 |
2243.7 |
1825.6 |
2194.8 |
2394.1 |
2258.4 |
2177.9 |
Blue Lava |
1774.4 |
2389.6 |
2389.6 |
2389.6 |
2390.5 |
1934.6 |
2226.8 |
2366.0 |
1789.1 |
2273.5 |
2192.5 |
1888.7 |
2356.7 |
1954.1 |
2085.4 |
2390.5 |
2124.1 |
2229.0 |
2394.1 |
2108.9 |
2394.1 |
Regular Clear |
1888.3 |
2335.8 |
2340.2 |
2389.6 |
2394.1 |
2394.1 |
2242.8 |
2394.1 |
2127.6 |
1602.3 |
2211.0 |
2185.9 |
2286.4 |
2033.8 |
1998.2 |
2144.1 |
2394.1 |
2279.7 |
2043.5 |
2350.5 |
2394.1 |
Rain-R-Shine |
2365.6 |
2186.8 |
2157.0 |
2389.6 |
2208.1 |
2394.1 |
2068.9 |
2394.1 |
2394.1 |
2394.1 |
2295.3 |
2124.1 |
2337.6 |
2212.6 |
2394.1 |
2394.1 |
2394.1 |
2394.1 |
2239.3 |
2069.3 |
2394.1 |
All Purpose |
2363.8 |
2389.6 |
2320.7 |
2359.8 |
2299.8 |
2394.1 |
1852.7 |
2034.2 |
2000.4 |
2383.4 |
2239.9 |
2522.6 |
2265.5 |
1799.3 |
2266.8 |
1984.8 |
2298.9 |
2230.4 |
2394.1 |
2301.1 |
2335.8 |
Compression Force (in Newtons) at Failure After 6 Hours |
Medium Gray |
2175.2 |
1786.4 |
2197.9 |
2098.3 |
2248.2 |
2317.6 |
2394.1 |
2394.1 |
2393.6 |
2393.6 |
2239.9 |
2182.3 |
2393.6 |
2117.8 |
2393.6 |
2380.3 |
2192.1 |
2394.1 |
1876.3 |
2335.4 |
2133.0 |
Blue Lava |
2389.6 |
2389.6 |
2389.6 |
2389.6 |
2391.8 |
buckled |
2324.2 |
2393.6 |
2393.6 |
2393.6 |
2384.4 |
2393.6 |
2391.8 |
2393.6 |
2391.8 |
2393.6 |
2391.8 |
2335.8 |
2391.8 |
2371.4 |
2391.8 |
Regular Clear |
2388.7 |
2389.6 |
2389.6 |
2389.6 |
1911.9 |
1751.3 |
2366.9 |
2393.6 |
2393.2 |
2393.6 |
2276.8 |
2257.1 |
2393.6 |
2338.9 |
2393.6 |
2185.4 |
2393.6 |
2279.3 |
2045.3 |
2389.2 |
2092.5 |
Rain-R-Shine |
2269.5 |
2062.2 |
2383.8 |
2373.6 |
1948.4 |
2393.6 |
2236.2 |
2393.6 |
2318.4 |
2393.6 |
2277.3 |
2076.5 |
2393.6 |
2217.9 |
2393.6 |
2248.2 |
2196.6 |
2334.5 |
2393.6 |
2279.3 |
2239.3 |
All Purpose |
2389.6 |
2389.6 |
2394.1 |
2394.1 |
2297.1 |
1899.0 |
1975.9 |
2392.7 |
2281.1 |
2393.6 |
2280.8 |
2355.8 |
2393.6 |
2394.1 |
2338.9 |
2026.2 |
2055.6 |
2168.5 |
2288.2 |
2394.1 |
2393.6 |
Compression Force (in Newtons) at Failure After 24 Hours |
Medium Gray |
2391.8 |
2391.8 |
2391.8 |
2391.8 |
buckled |
buckled |
2391.8 |
2391.8 |
buckled |
buckled |
2391.8 |
2391.8 |
2391.8 |
2391.8 |
2391.8 |
buckled |
2391.8 |
2391.8 |
2391.8 |
2391.8 |
2391.8 |
Blue Lava |
2391.8 |
buckled |
buckled |
buckled |
2391.8 |
2391.8 |
buckled |
2391.8 |
2391.8 |
2391.8 |
2391.8 |
2391.8 |
buckled |
2391.8 |
buckled |
buckled |
buckled |
2391.8 |
2391.8 |
2391.8 |
2391.8 |
Regular Clear |
2391.8 |
2391.8 |
2391.8 |
2391.8 |
2391.8 |
2391.8 |
2391.8 |
2391.8 |
2391.8 |
2391.8 |
2391.8 |
2391.8 |
2391.8 |
2391.8 |
2391.8 |
2391.8 |
2391.8 |
2391.8 |
2391.8 |
2391.8 |
2391.8 |
Rain-R-Shine |
2391.8 |
2391.8 |
2391.8 |
2391.8 |
2391.8 |
2391.8 |
2391.8 |
2391.8 |
2391.8 |
2391.8 |
2393.3 |
2391.8 |
2391.8 |
2395.4 |
2395.4 |
2395.4 |
2395.4 |
2395.4 |
2395.4 |
2395.4 |
2395.4 |
All Purpose |
2395.4 |
2395.4 |
2395.4 |
2395.4 |
2395.4 |
buckled |
2395.4 |
2395.4 |
2395.4 |
2395.4 |
2395.4 |
2395.4 |
2395.4 |
2395.4 |
2395.4 |
2395.4 |
2395.4 |
2395.4 |
2395.4 |
2395.4 |
2395.4 |
Graphs
* On graph 1.4, the joints are fully cured at 24 hours, and the compression forces needed for the joint failure exceeded the maximum capacity (2224.1 N) of the digital scale. The data recorded represents the maximum readings on the digital scale with small tolerances, but are obviously less than the true compression force at the moment of failure. However, a significant number of primed joints failed before the unprimed joints, as shown in table 1.1.
** On graph 1.5, the forces at failure of the joints are averaged across all the cements to allow for
a simple comparison between primed and unprimed joints to be visualized over time.
Torsion Test Results
Table 2.1 - Torsion Test
Time |
Primed |
Unprimed |
Primed |
Unprimed |
Primed |
Unprimed |
Primed |
Unprimed |
Primed |
Unprimed |
Average Torque |
Torque (in Newton-Meters) Failures Over Time |
2 Hours |
9.4 |
|
7.3 |
|
9.5 |
|
8.5 |
|
11.0 |
|
9.1 |
8.4 |
|
10.0 |
|
9.8 |
|
8.7 |
|
8.8 |
|
4 Hours |
15.2 |
|
|
12.0 |
13.4 |
|
14.4 |
|
13.0 |
|
13.2 |
13.2 |
|
15.1 |
|
|
12.8 |
13.5 |
|
14.2 |
|
6 Hours |
|
13.1 |
|
13.5 |
|
14.2 |
|
12.6 |
|
14.4 |
13.6 |
|
12.6 |
|
15.2 |
|
12.8 |
|
14.5 |
|
12.7 |
24 Hours |
22.2 |
|
|
20.3 |
18.3 |
|
twisted |
|
twisted |
|
20.3 |
20.1 |
|
|
20.5 |
twisted |
|
twisted |
|
twisted |
|
Graphs
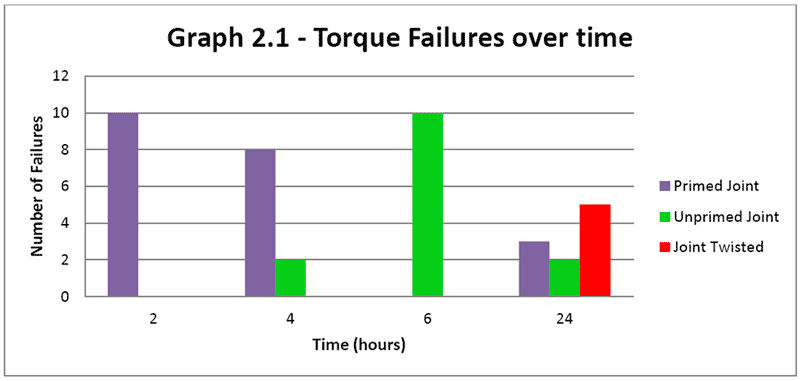
This graph shows the number of failures of either primed joints or unprimed joints over 24 hours.
Some joints twisted instead of failing because the joints were stronger than the actual plastic.
Photos
Figure 5 - Torsion test sample before failure
Figure 6 - Torsion test sample after failure
Figure 7 - Side view of failure
Figure 8 - Torsion test twisted sample
Figures 9 and 10 - Compression test sample
The sample was cut to examine the cross section of the joint, but no significant conclusions can be made from observation.
Figures 11 and 12 - Torsion test sample
The sample was cut to examine the cross section of the joint, but no significant conclusions can be made from observation.
Conclusion
The purpose of this investigation was to determine the effect of primer on the strength of solvent welded PVC and CPVC joints. Was primer necessary to have better joint strength? The hypothesis was that if primer penetrates and softens the plastic surfaces prior to the application of cement, then the inclusion of primer in the solvent welding process should achieve maximum fusion and strength. This was not the case. In both tests, the primer had a negative effect on the strength of the pipes. In the compression test, more primed joints failed first than unprimed joints. In the torsion test, the primed joints overall took less force to fail than the unprimed joints. The primed joints also had a higher failure rate, although the rates were more equal than in the compression test.
A reason why the primed joints were weaker than the unprimed joints may be that the primer presoftens the plastic more than the cement alone, so the plastic may have taken significantly more time to cure in the primed joints.
Another reason why the primed joints were weaker than the unprimed joints may be that the cement may have needed to be applied immediately after the primer is applied to prevent the primer from drying. Because the application was a manual process, a few seconds of exposure to air that the primer had could have dried it such that it formed a barrier to the cement to prevent the two materials from fusing together with the help of the cement.
Yet another reason the primed joints were weaker than the unprimed joints may be that the primer presoftens the plastic more than the cement alone, so when the plastic hardens again, the molecular structure may have changed. The hardened plastic may not have the same strength as the original plastic material.
The final reason why the primed joints could be weaker than the unprimed joints could be that because the cement contains most of the same ingredients as the primer does, the primer may not have added any real benefit to the joint strength. The primer may have actually made the joint weaker. The concentration of these ingredients in the cement alone may be more conducive to making a stronger joint than the concentration of the ingredients in both the primer and the cement combined. Therefore, cement alone may create a stronger joint than a two-step process of primer followed by cement. The manufacturer, Oatey SCS®, has been contacted, but so far no comments have been received.
While curing, the joints were not close to full strength. The manufacturer provided that the cure times for 1/2 in* sch. 40 PVC pipes from 60°F-100°F subjected to up to 180 psi are 15 min at most, but according to the test data, a fully cured joint at 24 hours is at least 30-50% stronger than the joint is at 2 hours. According to the manufacturer, the cure times for CPVC pipes are 1 hour at most. Based on the tests conducted at 2, 4, 6, and 24 hours, the strength increases greatly as time progresses, which is an indication that the cure time for the joints takes longer than the cure time suggested by the manufacturer. Most plumbers in the field would pressurize and test the system 15-30 minutes after solvent welding. This means the premature testing in the field could potentially lead to unnecessary joint failures.
The strongest cement was the Medium Gray PVC cement. The weakest cement was the Regular Clear PVC cement. The cement that primer (negatively) affected the most was the Rain-R-Shine® Medium Blue PVC cement.
There are many practical applications of this experiment. This investigation is of value to the plumbing and engineering community as it provides an answer to a highly debated subject. Many people have argued about whether primer serves a positive purpose in solvent welding on professional plumbing forums. There are differing opinions based on previous experiences of plumbers. It is the standard method of assembly to use primer in solvent welded joints because IPC (International Plumbing Code), UPC (Uniform Plumbing Code) as well as most regional plumbing codes require it. Yet, many plumbers follow this method because of the requirement, not because of the belief that it creates a better joint. If primer does not make a stronger joint, then the step of applying primer can be skipped resulting in tremendous amounts of time and cost savings. This report attempts to prove one way or the other whether primer is an essential component of creating a strong PVC joint.
*This value cannot be converted to metric units because it is a nominal dimension that is more about compatibility and less about measurements.
Limitations
- Tests on hydrostatic pressure were not performed because the researcher had limited equipment and resources
- Environmental factors
- → Humidity
- → Barometric pressure
- → Thickness of pipes and fittings
- Joints were manually assembled, so slight inconsistencies in the following:
- → Length of pipes
- → Depth of insertion
- → Amount of primer and cement applied to pipes and fittings
- → Time elapsed between primer application and cement application
- Digital scale failed to record force after capacity was exceeded
- Some failures of joints were not abrupt failures but slower plastic failures
Future Research
- Test for hydrostatic pressure
- Tests to be performed in a more controlled environment
- Investigate possibility of machines performing the solvent welding process to eliminate inconsistency of handmade assembly process
- Test for more time intervals
- Test for more cement and primer types
- More sophisticated testing equipment, ex. Digital scale that has a substantially larger capacity than 2224.1 N (500 lb)
- Increase dry time for the primer prior to applying cement
- Use a microscope to study molecular structure of joints